Strong edge rounding, long service lives, good performance
Elements for interior fittings and air conditioners for railway technology, ceiling elements for operating theatres, sheet guide plates and storage air systems for printing machines – the question of how complex components can be made from simple sheets of metal is the specialty of KWM Karl Weisshaar Ing. GmbH. In order to machine the sheets precisely and economically, the Mosbach-based company puts its faith in state-of-the art, automated machinery. Here, high-quality tools for deburring and rounding edges are provided by boeck GmbH from Leipheim.
From the engineering to sheet metal machining, the joining and welding technology to the assembly and logistics, everything comes from a single source – KWM Karl Weisshaar Ing. GmbH is an expert in the field of metal and sheet metal machining throughout the entire process chain. The all-rounder and problem solver in the sheet metal sector with a team of almost 500 employees is a recognised partner of many industries such as the printing press, automotive, food industry, rail vehicle or general engineering sectors as well as the areas of cleanroom and medical technology. Every year, the company processes more than 5,000 tonnes of sheet metal from steel, stainless steel and aluminium to form what are in some cases highly complex components. It goes without saying that, in addition to efficient processes, top quality takes top priority.
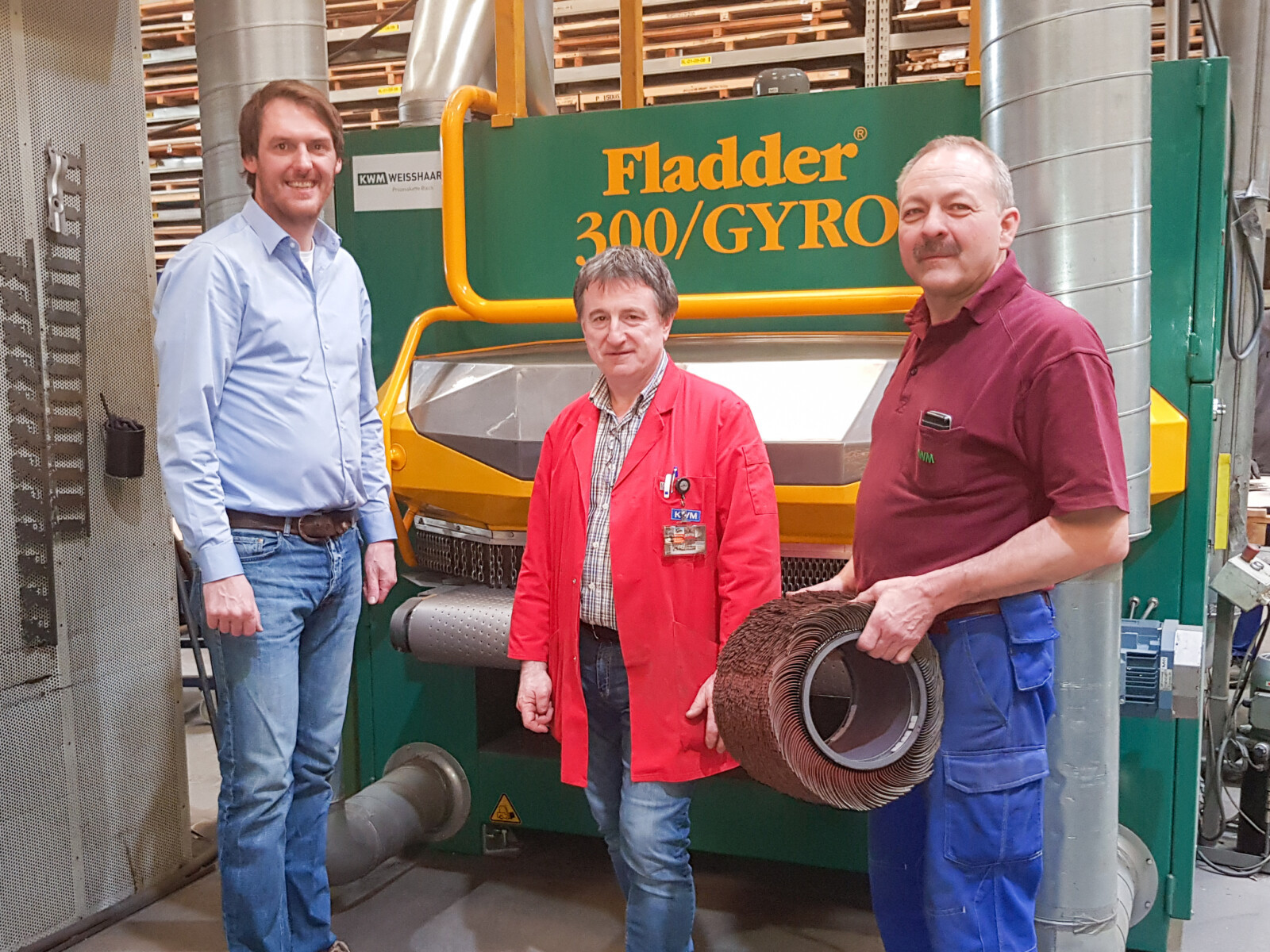
Partners for more efficient processes (from left): Marc Böck, Managing Director of boeck GmbH, Hans Schuster, Master of Laser Technology and CNC Punching Technology at KWM Weisshaar, and Jürgen Braun, Foreman in the Grinding and Deburring section at KWM Weisshaar.
Quality tools for sheet metal experts
Deburring and edge rounding are important steps in the process chain at KWM in view of the high demands placed on the production of the various components. They ideally prepare the laser-cut metal sheets for further processing. Among other things, the Mosbach-based company an automated FLADDER GYRO/300 deburring machine to this end. When employing this grinding technique, six grinding spindles rotate in opposite directions in pairs, simultaneously oscillating across the workpiece. “Thanks to this combination, the workpiece is machined continuously and evenly from alternating positions, almost without causing any damage to the surface. This enables a clean deburring and rounding of sheet metal parts – but only when you use the right tools,” states Hans Schuster, a master of laser technology and CNC punching technology at KWM Karl Weisshaar Ing. GmbH. “We have been using high quality deburring tools from boeck GmbH for some time – and not just for our FLADDER deburring machine.”
The innovative company from Leipheim is managed by the engineers Marc and Jochen Böck. The brothers and their team of experts develop and produce tailor-made tool solutions for sheet metal deburring – ranging from slag removal and rough grinding through deburring, edge-rounding and oxide removal to surface finishing. “We manufacture our tools on machines we develop ourselves with a high degree of automation. Thanks to the structured high-performance processes, we are not only able to guarantee the highest quality, but also quickly deliver tailor-made solutions at the same time. Almost all orders are shipped the same day”, states Marc Böck Dipl.-Ing. (FH) Dipl.-Kfm. (FH) (Graduate engineer, graduate of business administration), Managing Director of boeck GmbH.
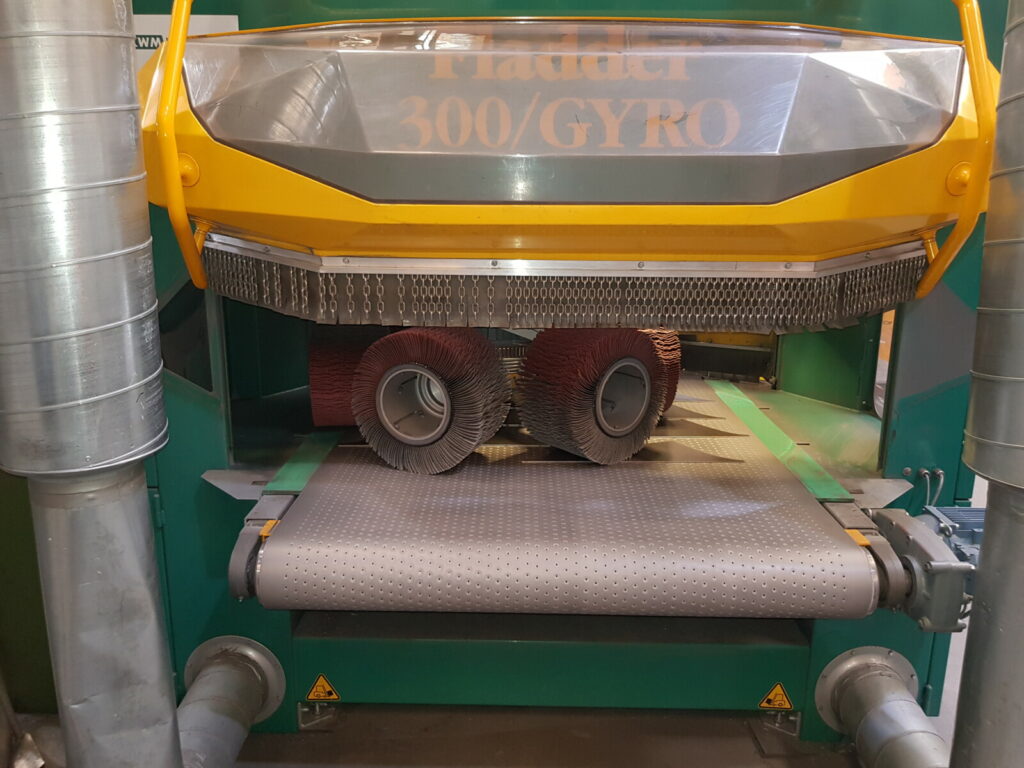
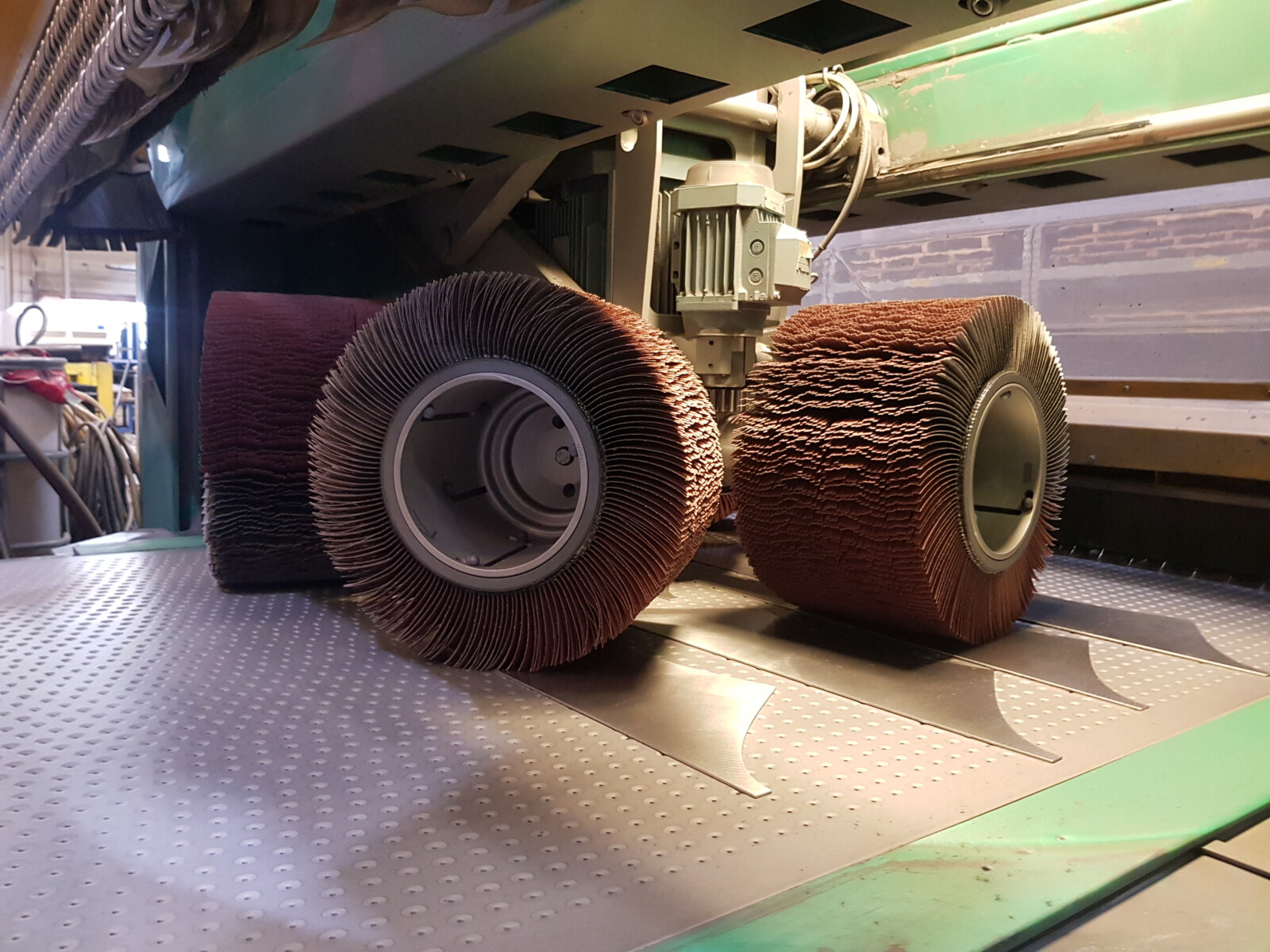
KWM Weisshaar uses the deburring roller 400x250x200mm from boeck on the FLADDER deburring machine, thus saving 50% of the machining time.
Due to the arrangement of the flaps in the grinding or deburring direction, KWM achieves an improved level of edge rounding than with the tools previously used.
Improved edge rounding while simultaneously reducing process times
Specifically for use on FLADDER deburring machines – in addition to other machine types – boeck has a variety of tools in its portfolio. On the FLADDER machine, KWM Weisshaar uses the deburring rollers with a diameter of 400 mm, a width of 250 mm and a receiving bore of 200 mm, thus achieving the best results in this way. Hans Schuster: “The deburring rollers provide very good levels of performance – whilst offering optimum value for money. We thus achieve a much improved level of edge rounding than with the tools previously used,” says Hans Schuster. Jürgen Braun, foreman in the grinding and deburring section at KWM Karl Weisshaar Ing. GmbH, is also enthusiastic: “In the past, we had to run the metal sheets through our FLADDER deburring machine four times to ensure sufficient levels of edge rounding, now we only have to do it twice. This saves on 50 per cent of our machining time!”
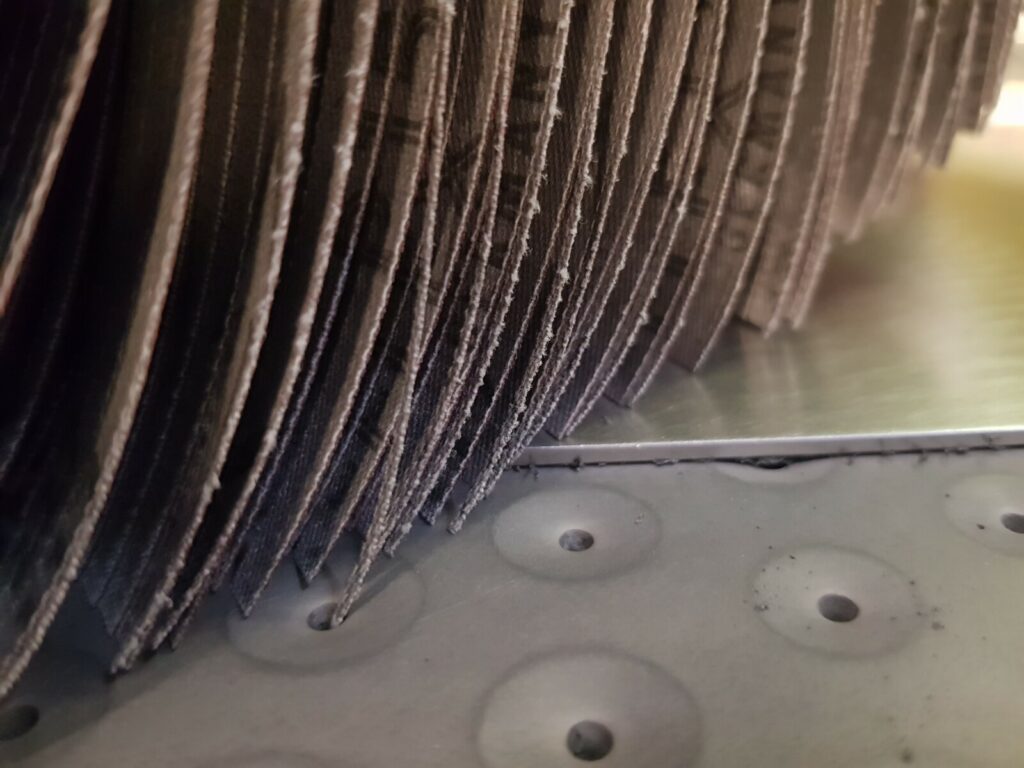
But what is so special about the deburring rollers? The individual abrasive cloth flaps are cut in a contactless manner via lasers. As a result, there are no grain losses in the abrasive cloth, as is the case with punching, for example. boeck deburring rollers have a very high abrasive cloth content. In addition, the flaps are arranged in the grinding or deburring direction and can be worn down to the core diameter. This results in long service lifes. At the same time, the deburring rollers are very light, despite the high abrasive fabric density. “This simplifies the handling when changing tools,” adds Jürgen Braun.
An additional quality characteristic: The deburring rollers are made of one piece without segmentation and therefore very sturdy. For smooth running, they are also balanced to the balance quality of G6,3.
The individual abrasive cloth flaps are cut in a contactless manner via lasers. This results in no grain losses in the abrasive fabric.
Different versions for different requirements
Depending on the workpiece range and the desired result, the user can choose between different types of abrasive cloth at boeck. Hans Schuster: “The standard version ‘Brown Edition’ is perfect for our requirements.” The all-rounder is suitable for all types of sheet metal. This allows us to machine the workpieces that change according to the job, without having to change the tools.” In addition, boeck offers even more different versions: For example, edges on components made of aluminium and plastic are ideally rounded with the “Grey Edition”. Customers requiring a very high removal rate or a marked level of edge rounding should resort to the “Purple Edition”.
All variants are available with different, slit patterns specially developed by boeck for different requirements. A higher level of contact pressure and a longer service life can be achieved depending on the slit used. Boeck also has the right solution for edge rounding of small cutouts and holes or in the event that the flaps are not supposed to appear to be quite as aggressive at the start.
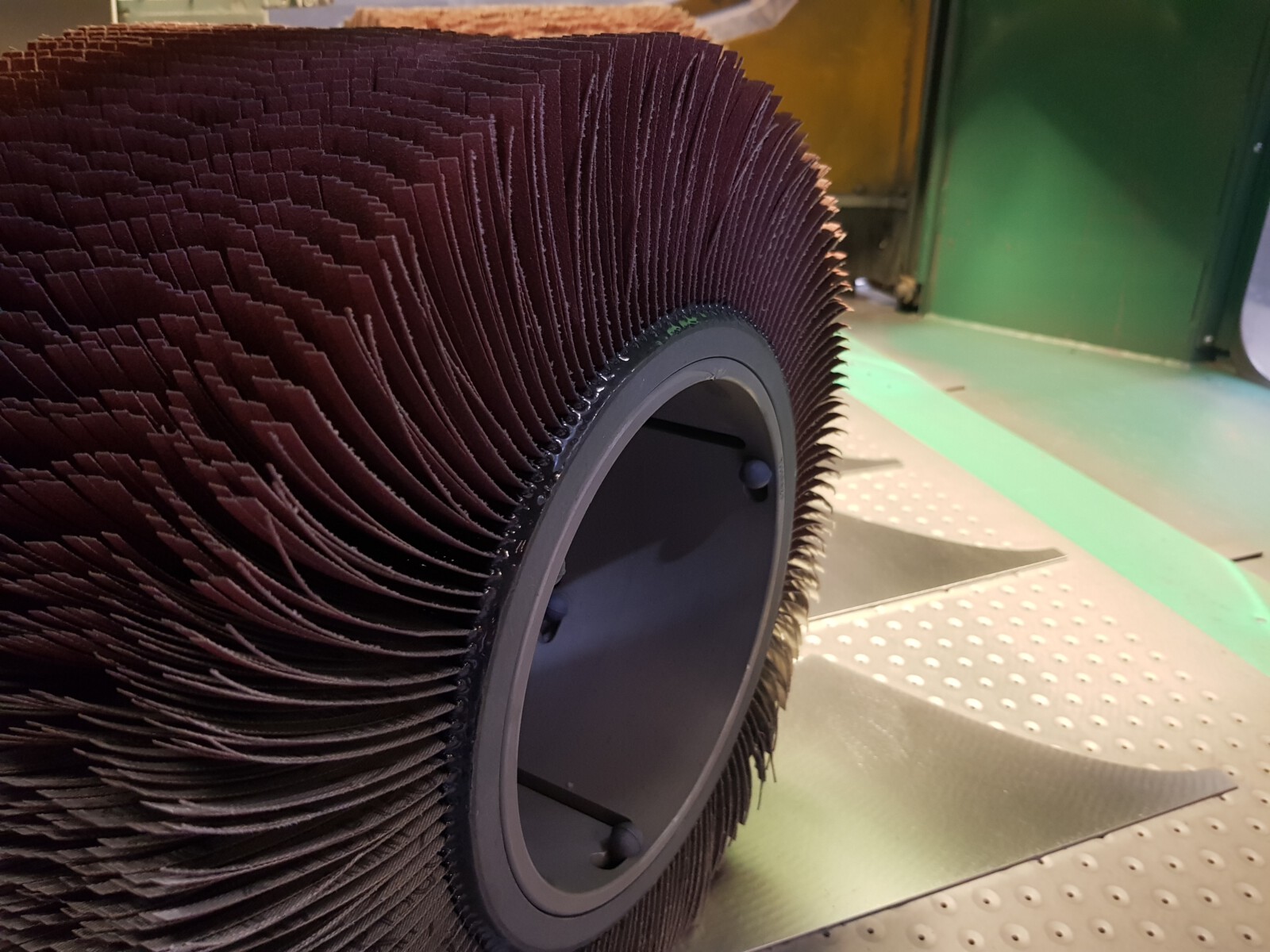
Despite the higher abrasive fabric content, boeck’s deburring rollers are very light. This reduces the bearing loads in the machine.
Partner for innovation
KWM Weisshaar is open to new technologies in order to achieve ever greater time, quality and cost benefits for the customer. Thus, a very special partnership has developed between the two companies: “KWM Weisshaar and not least Hans Schuster and Jürgen Braun have always been interested in new products. With its very large, modern machinery for grinding and deburring, the company is able to put our abrasives to the acid test before they are used. At KWM, we receive constructive feedback within a very short space of time”, states Marc Böck.
Hans Schuster also views boeck as more than just a simple tool supplier. “The company is instead an innovative development partner to make our grinding, deburring and oxide removal processes even more efficient. We also like to test boeck’s innovative product ideas in terms of their suitability for everyday use and have already had many positive experiences with it.”
Save 50% of your processing time?
Click here to discover our products.
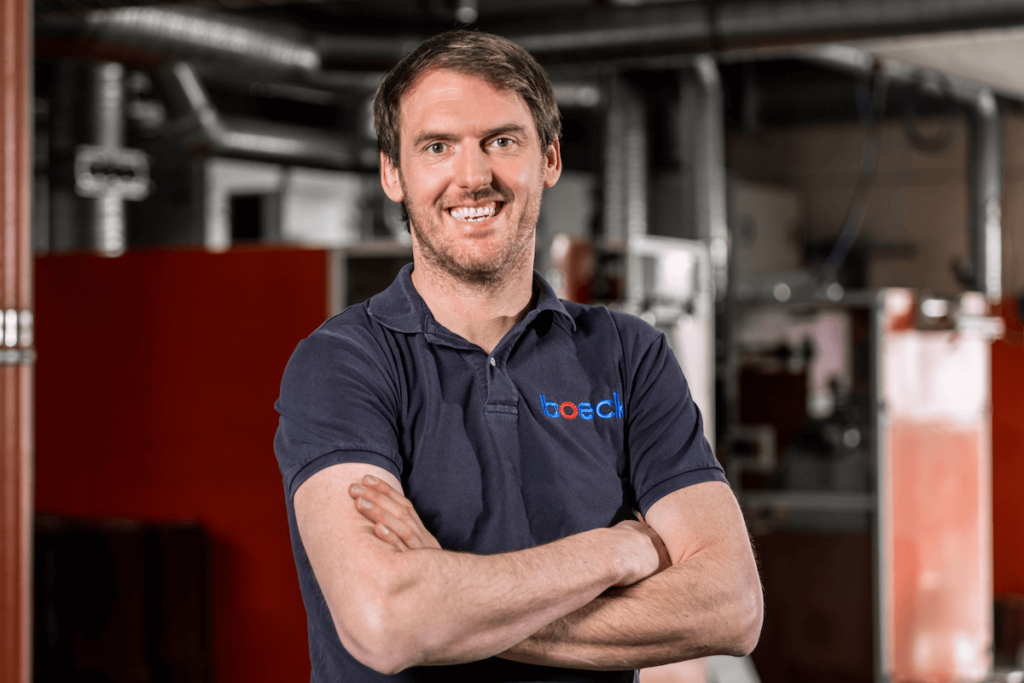
