TECHNOLOGY
Optimal production processes are only possible with perfect tools. This is exactly the goal for which boeck is constantly developing new tool solutions that set new standards.
01
DESLAGGING
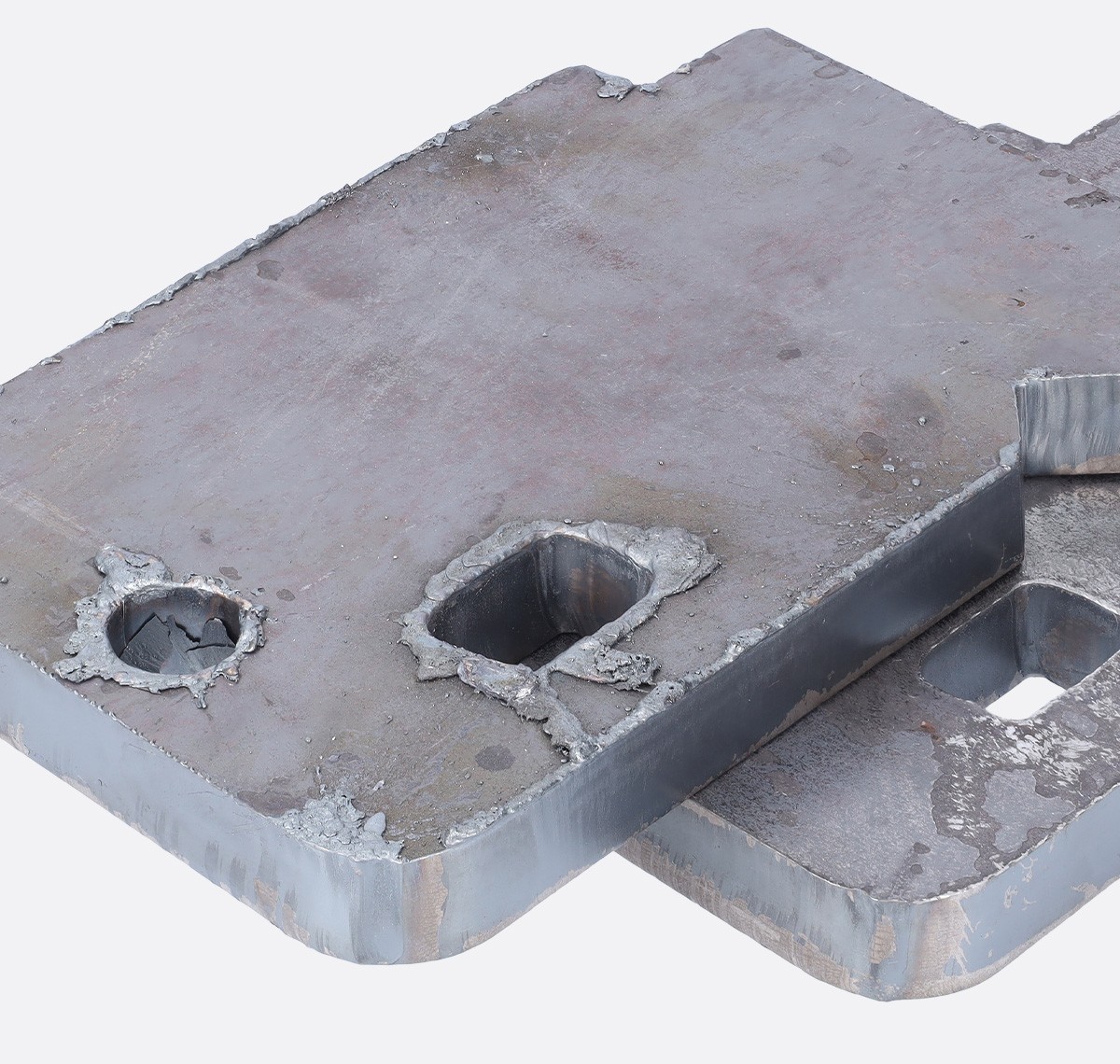

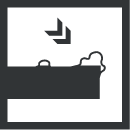
With plasma or oxy-fuel cutting, there is often strong melting and sagging of the melt on the beam exit side. The so-called slag occurs on both the inner and outer contours of the component and must be removed for further processing.
Common manual methods of slag removal are knocking them off with a hammer and chisel or grinding with an angle grinder. In the mechanical area, excess material accumulations can be removed by grinding with a soft contact roller. Another industrial method is knocking off using a slag hammer brush, which consists of a large number of flexibly mounted pins.
On our website in the knowledge & news section, we share additional information to improve your processes.
02 PRE-GRINDING &
DEBURRING
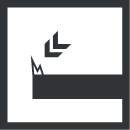
In the case of laser, plasma and oxy-fuel cut or punched sheet metal parts, the formation of burrs can often not be avoided. The ridge or primary ridge is a material structure on the cutting edge of components that protrudes beyond the original workpiece edges and surfaces. Further deviations from the target state are, for example, splashes on the component surface caused by laser cutting, unevenness or scaling of the surface. A by-product of the primary burr removal is the so-called secondary burr. This extends in the direction of the component surface and is caused by insufficient removal and simultaneous reshaping of the residual material.
Primary burrs, spatter, unevenness and/or layers of scale are usually removed by grinding. When removing primary burrs, the focus is also on minimizing secondary burr formation. In order to remove the undesired secondary properties on the sheet without leaving any residue, special carrier systems for sanding belts, discs or bows are required.
On our website in the knowledge & news section, we share additional information to improve your processes.


03 DEBURRING & EDGE-
ROUNDING
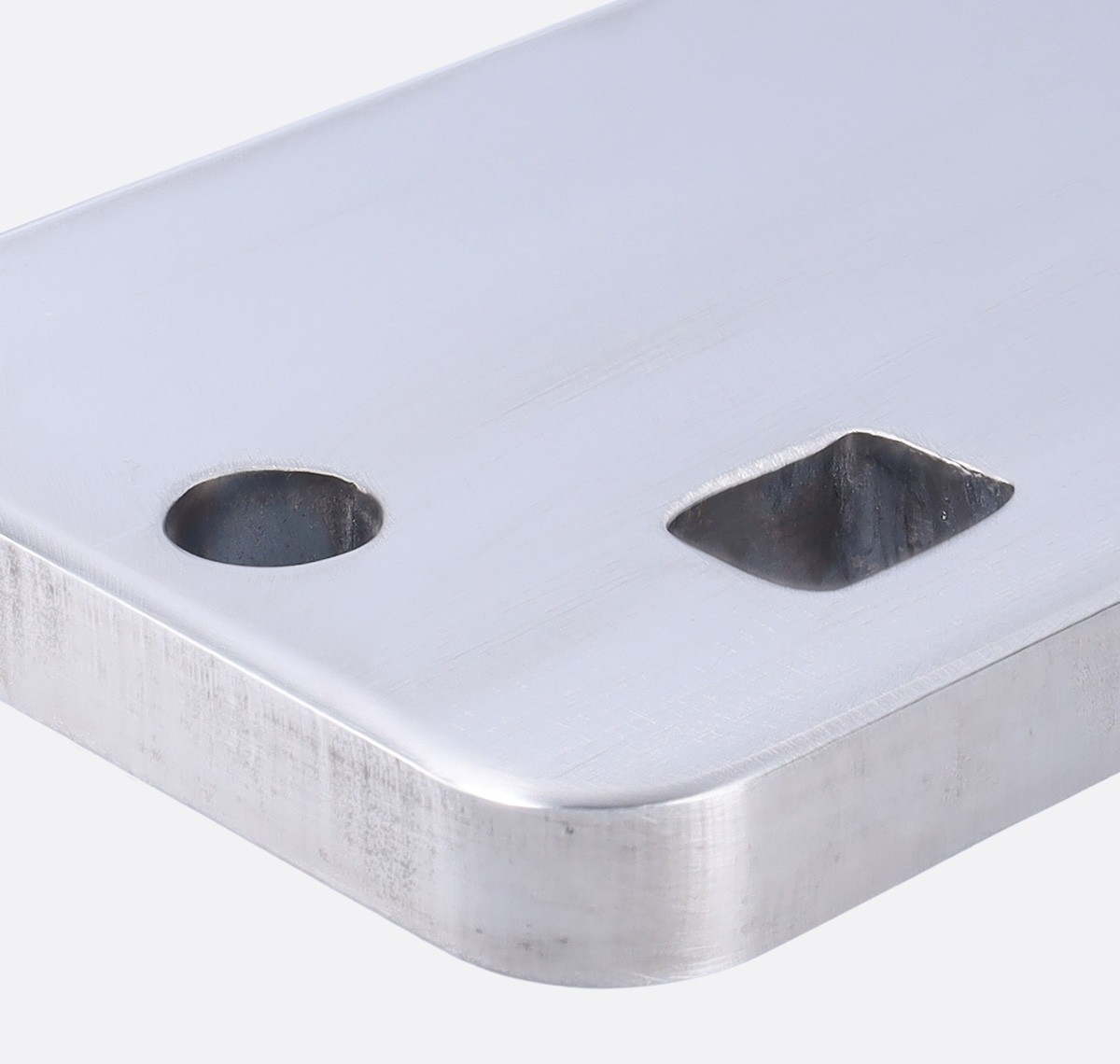

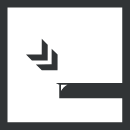
In this process step, the primary and secondary burrs are removed and the edges rounded. In order to create the prerequisites for subsequent process steps (powder coating, wet painting, electroplating, anodizing, etc.) and to exclude the risk of injury from sharp edges, the removal of the primary or secondary burr is often combined with the so-called edge rounding. The curves range from a few tenths of a millimeter to radii of 2 mm or even larger. These radii are now used by standards such as DIN EN 1090.
Deburring and edge rounding is carried out using flexible abrasive tools with high adaptability to inner and outer contours such as radii, holes and cutouts. The corresponding deburring discs, deburring rollers, deburring blocks and deburring brushes are used on hand machines as well as grinding and deburring machines. The latter have, for example, planetary head systems or oscillating units for even processing of the edges.
On our website in the knowledge & news section, we share additional information to improve your processes.
04 OXIDE REMOVAL
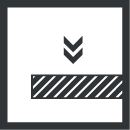
Components cut with oxygen have oxide layers on the cut edges. These dark layers pose a risk of adhesion for subsequent processes. For example, they can lead to the coating flaking off and must therefore be removed.
The oxide layer is mechanically removed by grinding or brushing. Both machining options can be used in manual machining processes. In the field of machine processing, brushes are mostly used which, thanks to specially developed wire trimmings in an innovative multi-row arrangement, flexibly follow the component contours and achieve shiny metallic edge surfaces.
On our website in the knowledge & news section, we share additional information to improve your processes.
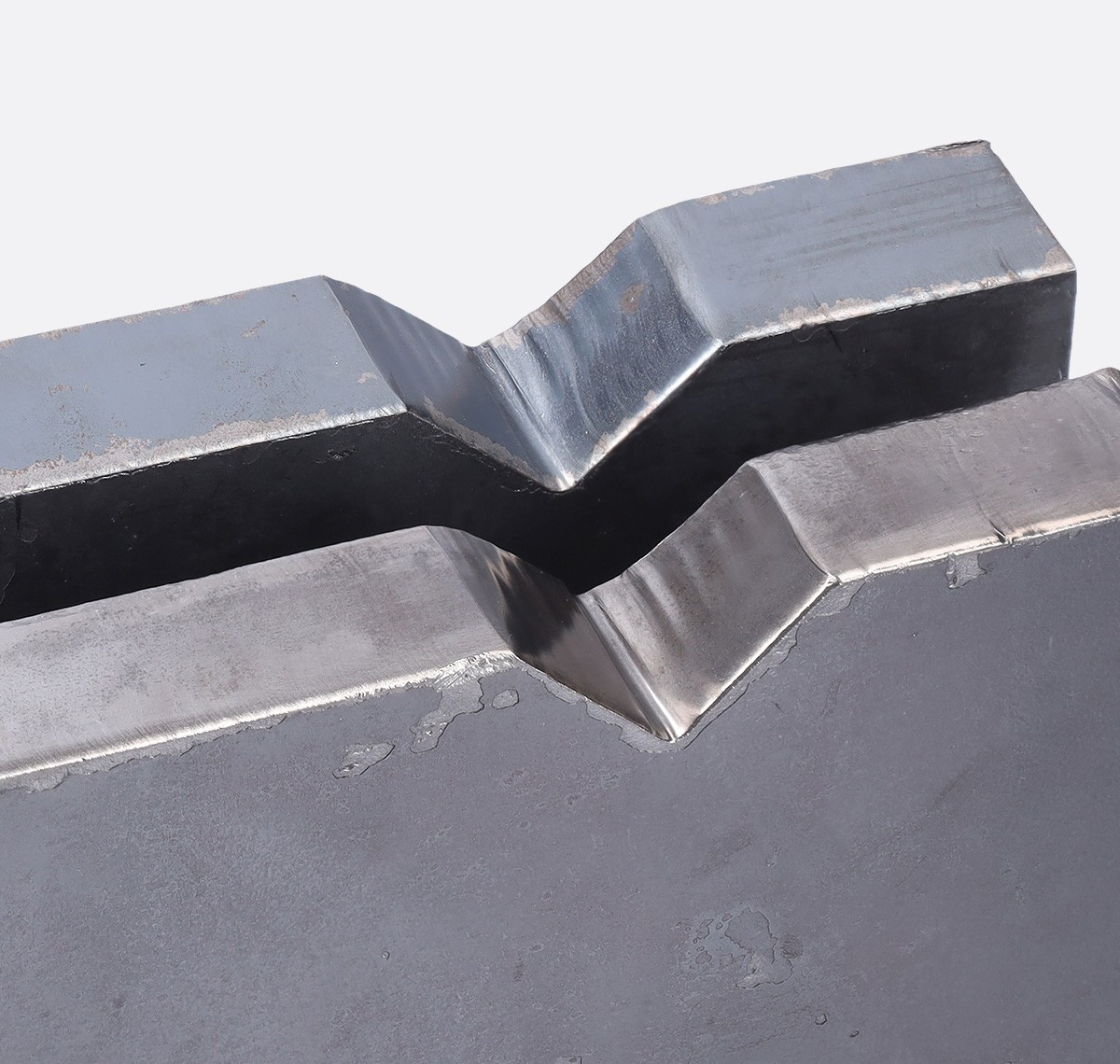

05 FINISH-GRINDING
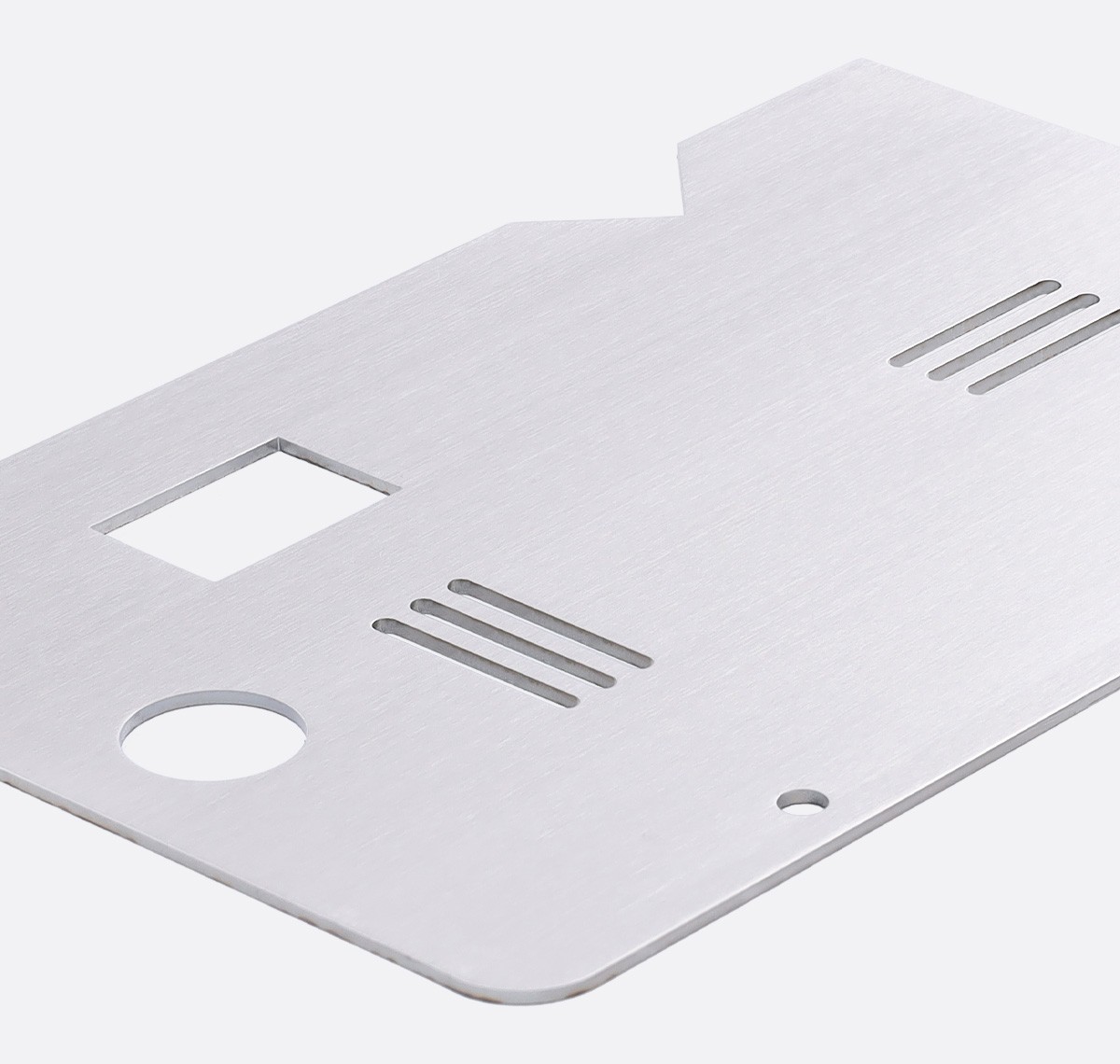

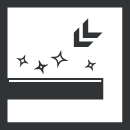
This process step serves to grind out scratch marks and to produce a decorative surface. Certain grinding patterns up to a high-gloss mirror finish can be achieved on the sheet surfaces.
In the final processing step, mainly abrasive fleece, abrasive cloth and felt tools are used as a continuous belt or as a roller. In manual finishing processes, the result and reproducibility depend to a large extent on the operator. In machine finishing, the machine must have appropriate adjustment options (e.g. stationary abrasive belt).
On our website in the knowledge & news section, we share additional information to improve your processes.