If you want to reduce costs in manufacturing without sacrificing quality, you often have only one set screw: shorter process times. De facto, this means that setup times must be reduced. When deburring and edge rounding its semi-finished steel and stainless steel products, Blokland Metalbewerking B. V. has achieved amazing results in terms of non-productive time by switching to the boeck deburring block system. The Dutch company saves up to 80 percent of the set-up times, requires fewer tools and has once again increased the quality of the deburred sheets.
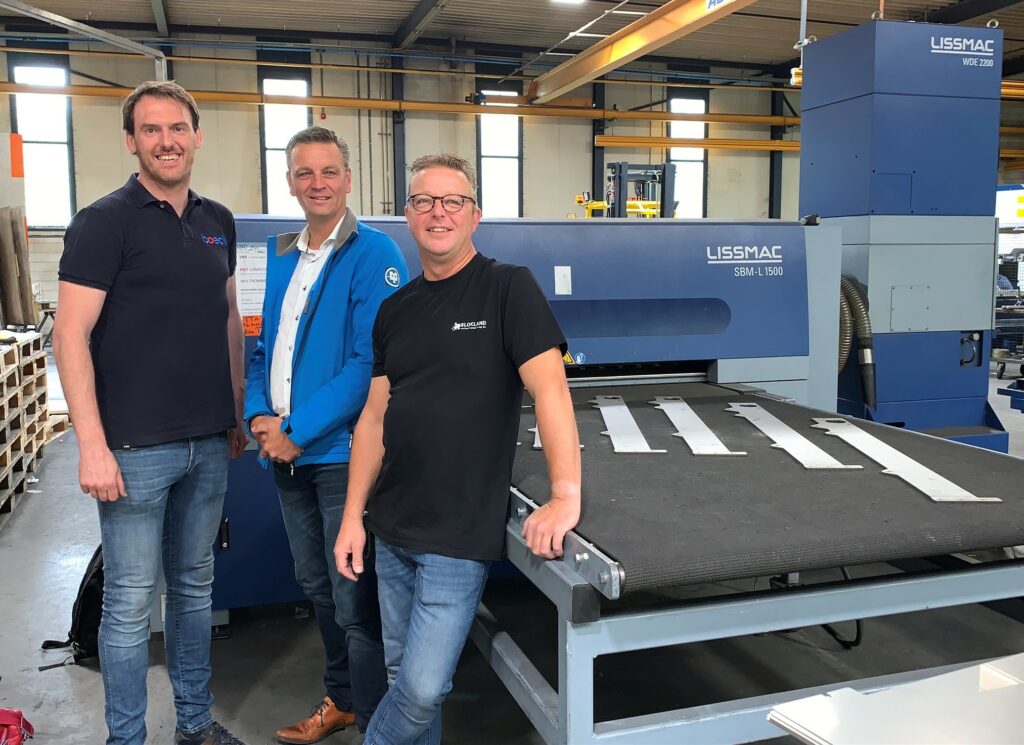
Marc Böck, Managing Director of boeck GmbH, Cor Schoonbeek, Technical Sales at Metaaltechniek Handelsonderneming B.V., and René Kruidhof, Plant Manager at Blokland Metalbewerking B.. V., (from left) optimized the deburring processes at Blockland together – with fantastic results.
In the Dutch town of Hardinxveld-Giessendam, everything revolves around metal. For more than 50 years, Blokland Metalworking B. V. has been known as a specialist in the production of high-quality semi-finished products made of ferrous materials and non-ferrous metals. Tube laser, laser and water cutting, punching, edge bending, milling, turning as well as assembling – thanks to the modern machinery with a high degree of automation, the company can flexibly meet all requirements. To ensure the high quality of the metal parts, deburring and edge rounding are important steps in Blokland’s production process. “Our customers – especially from the food industry – have the highest demands when it comes to edge rounding of their sheet metal parts. With our two LISSMAC SBM-L 1500 deburring machines, we can meet these requirements with confidence. We use one machine for steel and the other for stainless steel. Every month, we deburr about 50 tons of stainless steel sheets. Highest productivity is an absolute must,” says René Kruidhof, plant manager at Blokland Metalbewerking B. V. “The advantage of the LISSMAC machines is that we can simultaneously machine all cutting contours at the top and bottom in a single operation. This ensures efficient machining times and also precise as well as reproducible quality. The machines are perfect for our requirements, but we definitely saw potential for optimization in the deburring tools. In the end, however, we were impressed by how great this would be.”
Bundled competence for the perfect solution
In search of ways to further improve deburring and edge rounding on the two LISSMAC machines, Blokland turned to Metaaltechniek Handelsonderneming B.V. The technical wholesaler from Amersfoort, the Netherlands, has over 50 years of experience in all aspects of grinding and polishing processes and works very closely with boeck GmbH on the Dutch market. The team of experts around engineers Marc and Jochen Böck put their heart and soul into developing and producing customized tool solutions for sheet metal deburring – from slag removal and pre-grinding to deburring, rounding, oxide removal and surface finishing. This combined expertise in grinding and deburring technology provided the perfect starting point for Blokland.
The experts from boeck and Metaaltechniek Handelsonderneming are in constant exchange about technical innovations and challenges. “The LISSMAC deburring machines work with flexible deburring blocks on a power belt. It quickly became clear to us that the boeck system would bring enormous savings in setup time and also an improvement in performance for Blokland,” agree Cor Schoonbeek, Technical Sales at Metaaltechniek Handelsonderneming B.V., and Marc Böck, Managing Director of boeck GmbH.
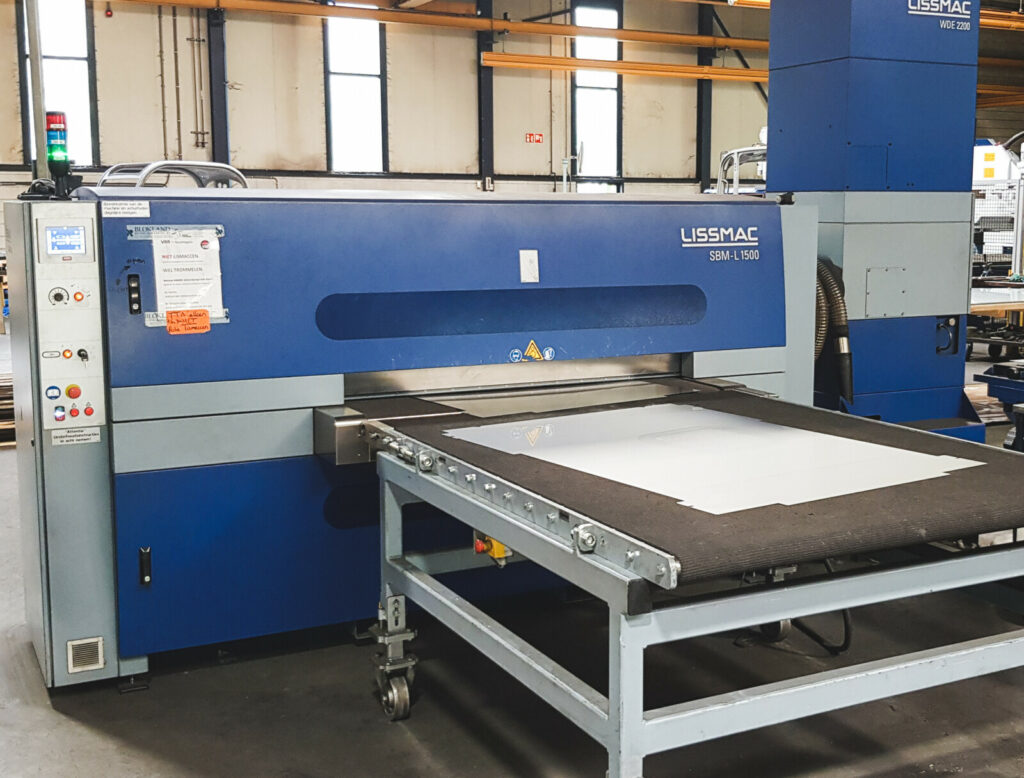
Deburring machines are perfectly suited for the requirements of Blokland. With boeck’s deburring blocks, the quality of edge rounding could be improved, set-up times minimized and tooling costs reduced.
Set-up times at the minimum
In order to change the original tools from LISSMAC, the machine operator has to unscrew the old deburring blocks after removing the four power belts – two for the top and two for the bottom – and screw the new ones back on individually. “Quite a bit of time passes before all the deburring blocks are replaced,” Marc Böck knows. “In order to drastically reduce this time for the user, we have developed our quick clamping system. Basic carrier blocks are already pre-mounted on our kraftbands. When changing tools, the red deburring blocks simply have to be clicked out or in. It’s a matter of seconds.”
René Kruidhof is enthusiastic: “When the experts presented the boeck deburring blocks to us for the first time, we were immediately hooked. In use, the system then far exceeded our expectations. The innovative quick-clamping system enables us to change the deburring blocks in the shortest possible time. This allows us to reduce setup times by almost 80 percent! That’s fantastic! Not only does it allow us to minimize machine downtime, but our employees can now use the time gained for value-added work.”
And that’s not all: due to the continuous disassembly or assembly of the deburring blocks, the bores in the kraftbands in the LISSMAC system are subjected to high stress and wear. This means that the belts have to be replaced regularly. With the boeck system, this wear is completely eliminated. In addition, the boeck deburring blocks are slightly longer, so that approximately ten percent fewer tools are required overall compared to the original. “So in addition to the set-up times, we can save costs again directly – and all with one system. That’s something that has to be duplicated,” says a delighted René Kruidhof.
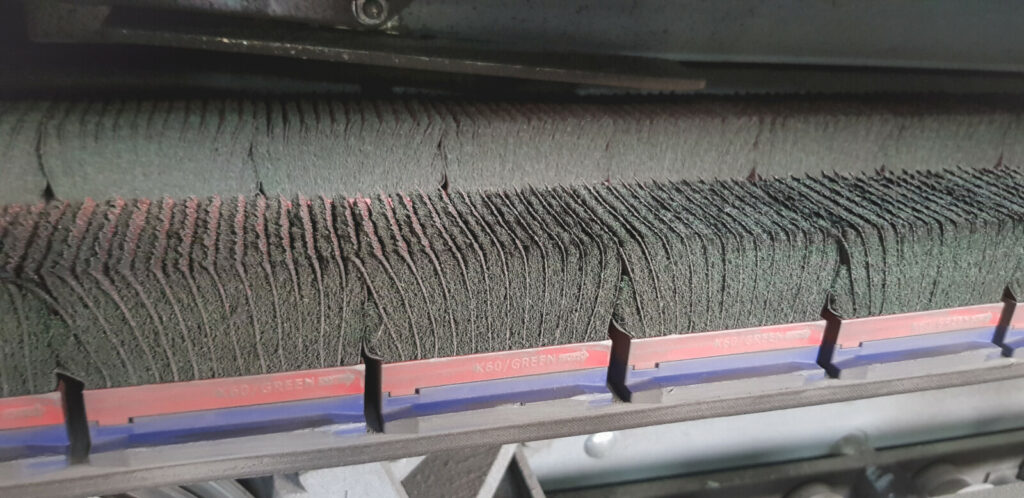
boeck has developed a universal deburring block system for LISSMAC and NS-MAQUINAS deburring machines. With a large portfolio of different tools, boeck has the right solution for a wide range of applications.
Excellent quality on top
one who now thinks that Blokland might have to compromise on performance and quality with the boeck deburring blocks is far wrong. René Kruidhof comments: “The tools from boeck are state of the art. This ensures both long tool life and consistently high performance. This has enabled us to significantly increase the quality of sheet metal edge rounding once again, while further reducing costs.” In addition, boeck, with its many years of know-how, supports Blokland – as it does all its customers – in the selection of the appropriate machine and tool parameters, such as cutting and feed speeds, in order to achieve the best possible results.
Marc Böck: “The LISSMAC machines pose two particular challenges for the tools: On the one hand, high removal rates are required because of the relatively short contact zone of twice 50 mm, and on the other hand, the kinematics of the deburring machine make it difficult to achieve uniform edge rounding on the sheet edges. We have developed our deburring blocks specifically for these deburring machines and have a large portfolio for the various requirements.”
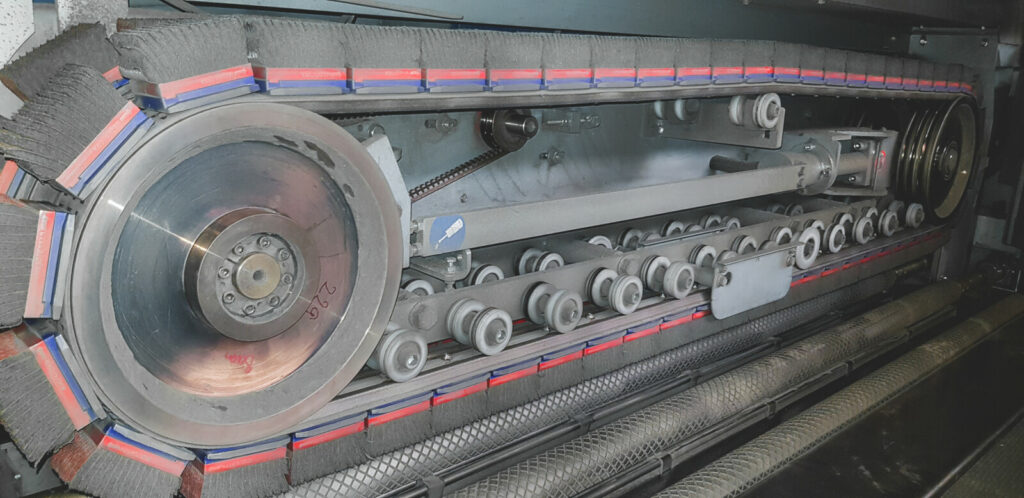
When changing boeck tools, simply click the red deburring blocks out of or into the blue base bodies. This novel quick-clamping system reduces the set-up times at Blokland by up to 80 percent!
Large selection with short delivery times
The standard deburring blocks are available in a wide variety of designs: The GREEN EDITION can be used for all sheet metals due to its adaptability. While the BLUE EDITION is mainly used for stainless steel sheets, the GREY EDITION is excellently suited for components made of aluminum and plastic. Both variants offer an additional highlight: thanks to the special grain geometry, the sheet surface is given a glossy effect. The deburring blocks of the individual editions can also be equipped with a more powerful abrasive cloth. This results, for example, in greater edge rounding. Users achieve the highest possible stock removal rate with the HERO deburring blocks. They consist purely of abrasive cloth flaps in finger structure and impress with their very hard backing material combined with extreme flexibility. This ensures the very high edge rounding that is often desired.
“Whether standard or HERO variant – we can additionally tailor the deburring blocks precisely to the respective application. For example, we enable our customers to achieve the largest possible edge radii on sheet metal parts or even high-speed deburring,” adds Marc Böck. In addition to the innovative deburring block system, boeck GmbH also offers the matching abrasive cloth belts for removing primary burrs for all LISSMAC machines. In addition to different grit sizes, the user has the choice here between different abrasives: for universal use, for a fine grinding pattern with high cutting ability or for high material removal with low processing temperature, long service life and optimum surface quality. Whether deburring block or abrasive cloth belt – thanks to a coordinated production strategy and intelligent stock-keeping, boeck can deliver the right tool from stock within a very short time.
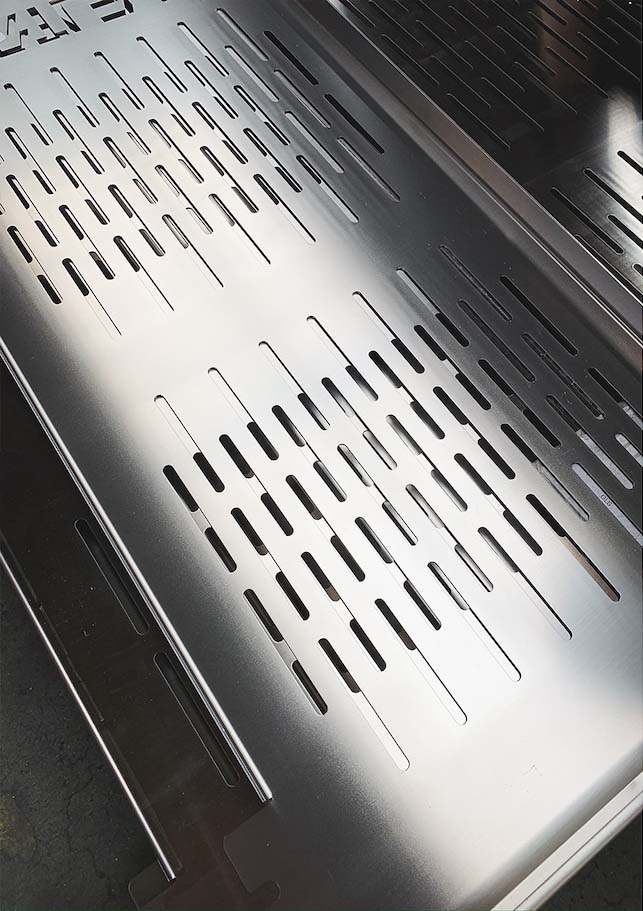
With the boeck deburring blocks, Blokland was once again able to significantly increase the quality of the sheet edges while further reducing tool costs.
Large selection with short delivery times
The standard deburring blocks are available in a wide variety of designs: The GREEN EDITION can be used for all sheet metals due to its adaptability. While the BLUE EDITION is mainly used for stainless steel sheets, the GREY EDITION is excellently suited for components made of aluminum and plastic. Both variants offer an additional highlight: thanks to the special grain geometry, the sheet surface is given a glossy effect. The deburring blocks of the individual editions can also be equipped with a more powerful abrasive cloth. This results, for example, in greater edge rounding. Users achieve the highest possible stock removal rate with the HERO deburring blocks. They consist purely of abrasive cloth flaps in finger structure and impress with their very hard backing material combined with extreme flexibility. This ensures the often desired very high edge rounding.
Shorten your set-up times!
Click here to discover our deburring blocks.
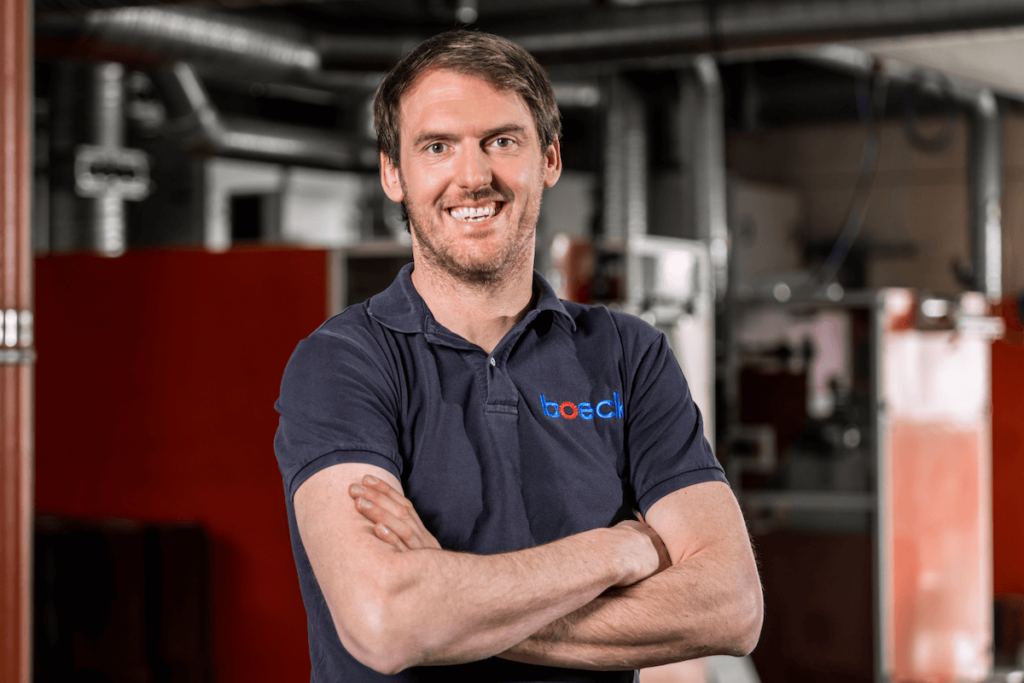
