DESLAGGING BRUSH BY BOECK
The slag is a product of plasma or flame cutting. It must be removed for the further processing of sheet metal. The deslagging brushes from boeck have been specially developed to make this work step as uncomplicated and efficient as possible.
DESLAGGING BRUSH BY BOECK
Our goal is to improve and streamline your entire sheet metal fabrication process. An essential part of this process is slag removal. In this process step, slag residues are knocked off. Our deslagging brushes do this in the most efficient way, reducing your machining time and costs.
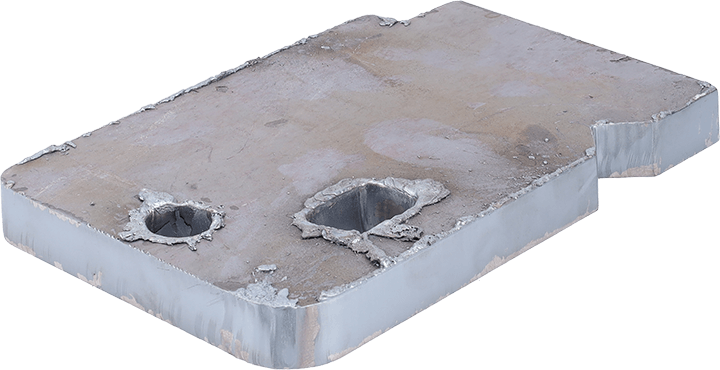
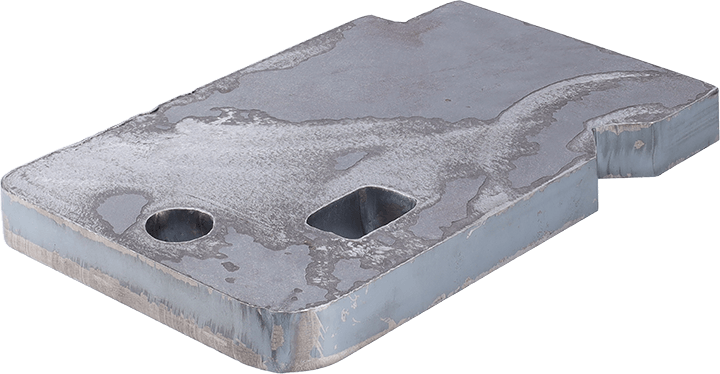
Deslagging with our deslagging brush
The slag produced during plasma or flame cutting is a by-product and must be removed for effective and economical further processing.
Conventional methods of slag removal include knocking it off with a hammer and chisel or grinding it with an angle grinder. However, this labor-intensive process step is very tedious and time-consuming.
This is where the boeck deslagging brush with its innovative design can help.
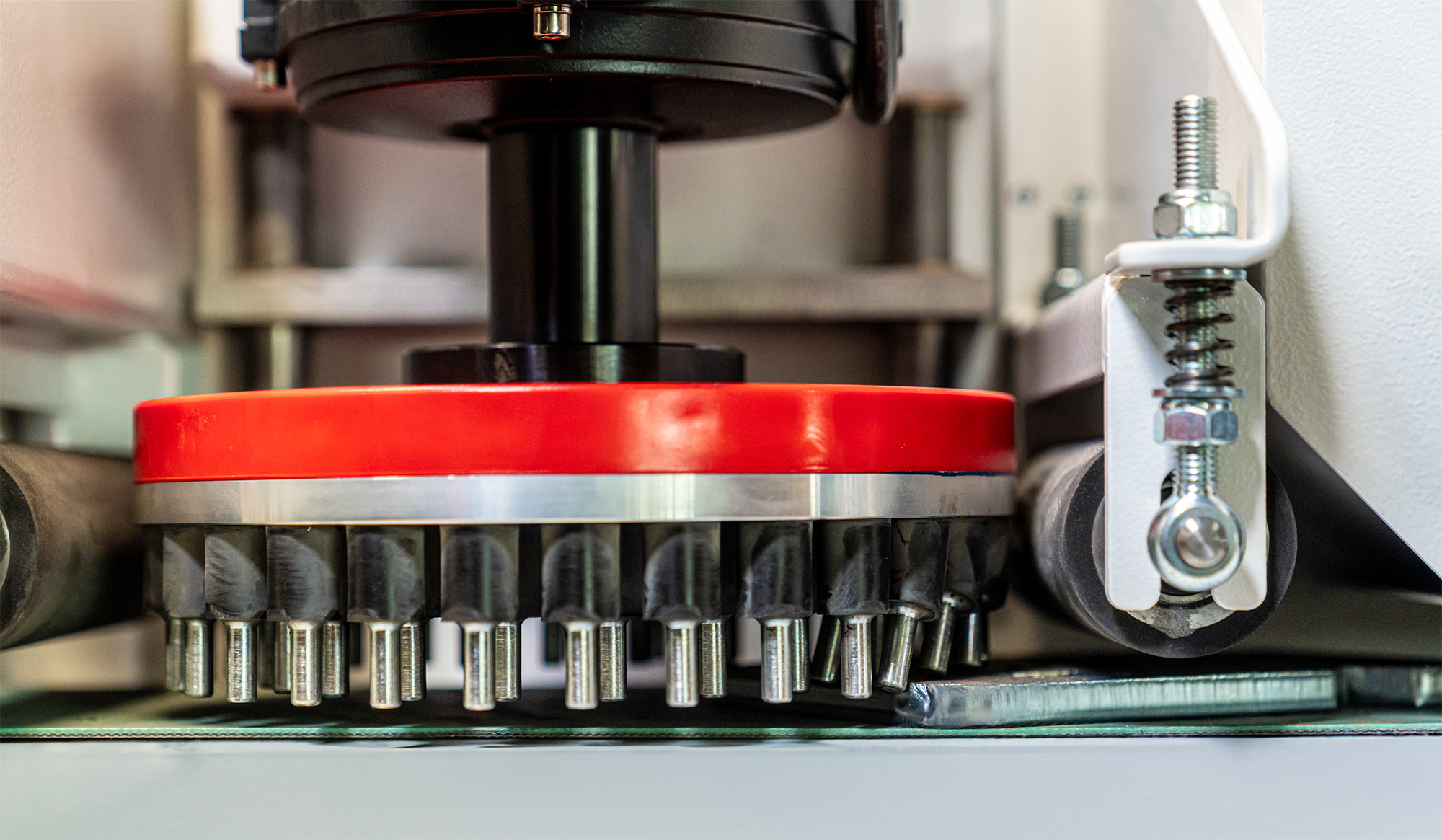
Why a deslagging brush?
Replace the classic hammer and chisel with the efficiency of boeck’s slag hammer brushes. These rotating brushes, equipped with hardened steel pins, quickly and effectively remove slag and deposits from metal surfaces. Compatible with most deburring and manual machines, they can be upgraded with our QUICK release system for faster, hassle-free setup.
Our brushes feature replaceable pins, eliminating the need to replace the entire tool due to wear. To meet varying needs, we offer different pin diameters and hardness levels (H1–H4), as well as single-row and double-row configurations for precise slag removal.
Need help selecting the right brush? Contact us for expert advice!
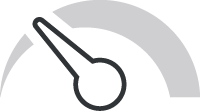
hammer and chisel

- Precise
- Labor intensive - risk of overload and injury
- Slow - long processing time
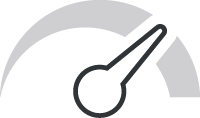
angle grinder

- Inaccurate - risk of removing too much material
- Labor-intensive
- Relatively fast
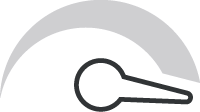
deslagging brush
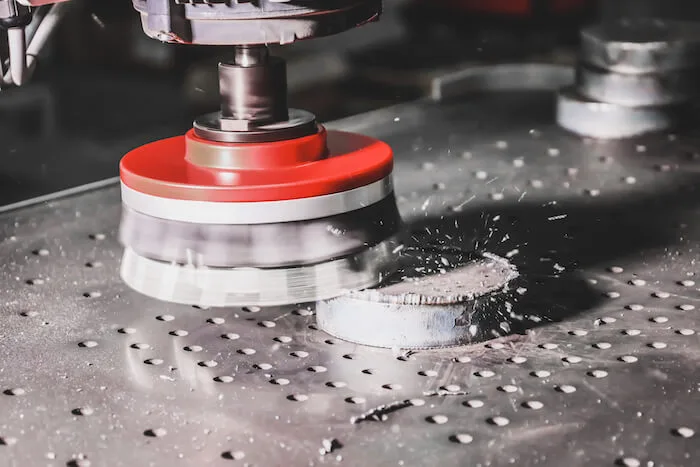
- Precise - removes only excess material
- Not labor intensive - safest processing
- Very fast - shortest processing time
Deslagging brush – also for Handheld machines
With the deslagging brush from boeck, you can reduce workpiece processing times to a minimum. Efficiency and a long service life are its greatest strengths.
The boeck deslagging brush is also excellently suited for use on hand-guided machines. It is easy to handle and requires minimal effort to remove slag and deposits from metal surfaces.
HARDNESS LEVELS OF OUR deslagging brush
H1 to H4
Deslagging brushes from boeck are available in four different degrees of hardness, determined by the hardness of the replaceable pins. This allows the deslagging tool to be matched to the workpiece and the toughness of the slag. In addition to the right deslagging brush, the optimum setting parameters are crucial for economical processing and best results. We will be happy to help you with this and are available for questions and recommendations.
H1
Very flexibly mounted pins – gentle on the edges! The soft slag hammer pins exert low pressure on the slag accumulations.
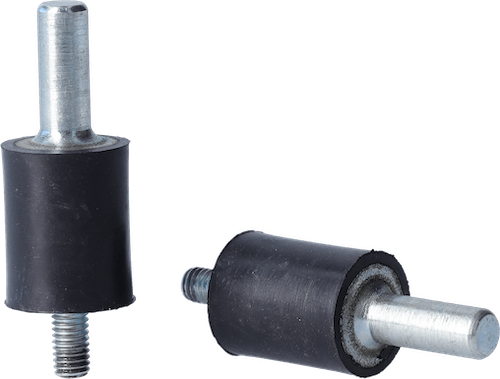
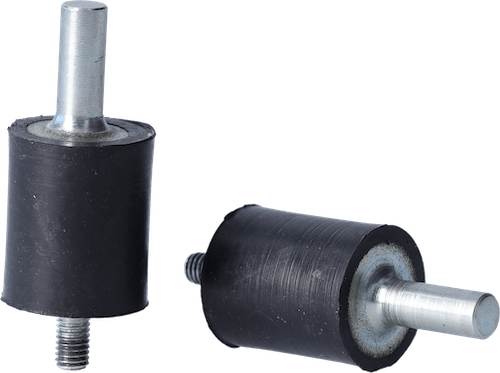
H2
Flexibly mounted pins – universally applicable! Stronger slag residues can be removed and at the same time workpiece edges are protected.
H3
Hard bearing pins – great impulse! Workpiece edges with stubborn slag residues can be removed with this slag hammer pin
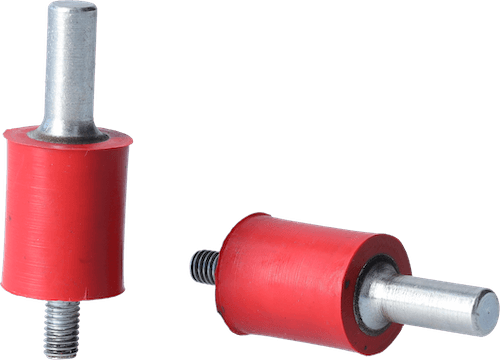
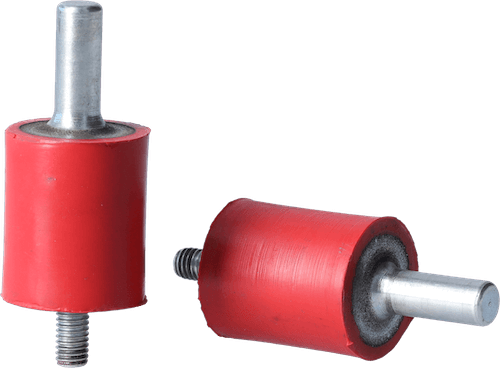
H4
Extra hard pins – maximum aggressiveness! The hard deslagging pins are used to remove extremely adherent slag residues.
Deslagging brush in action
OUR CUSTOMERS' BENEFITS
SAVINGS IN PROCESSING TIMES
Processing times can be reduced by tailoring the tools to fit customers' machines and projects. One customer application shows, that 80% processing time can be saved during deburring.
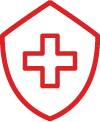
Ensure safety
Reduce labor intensity and other hazards during purification by eliminating manual hammering or grinding.
OPTIMIZING THE SHEET METAL PROCESSING CHAIN
Our customers benefit from our distinctive consulting and application expertise. This know-how guarantees maximum competitiveness through high-performance processes in every production.
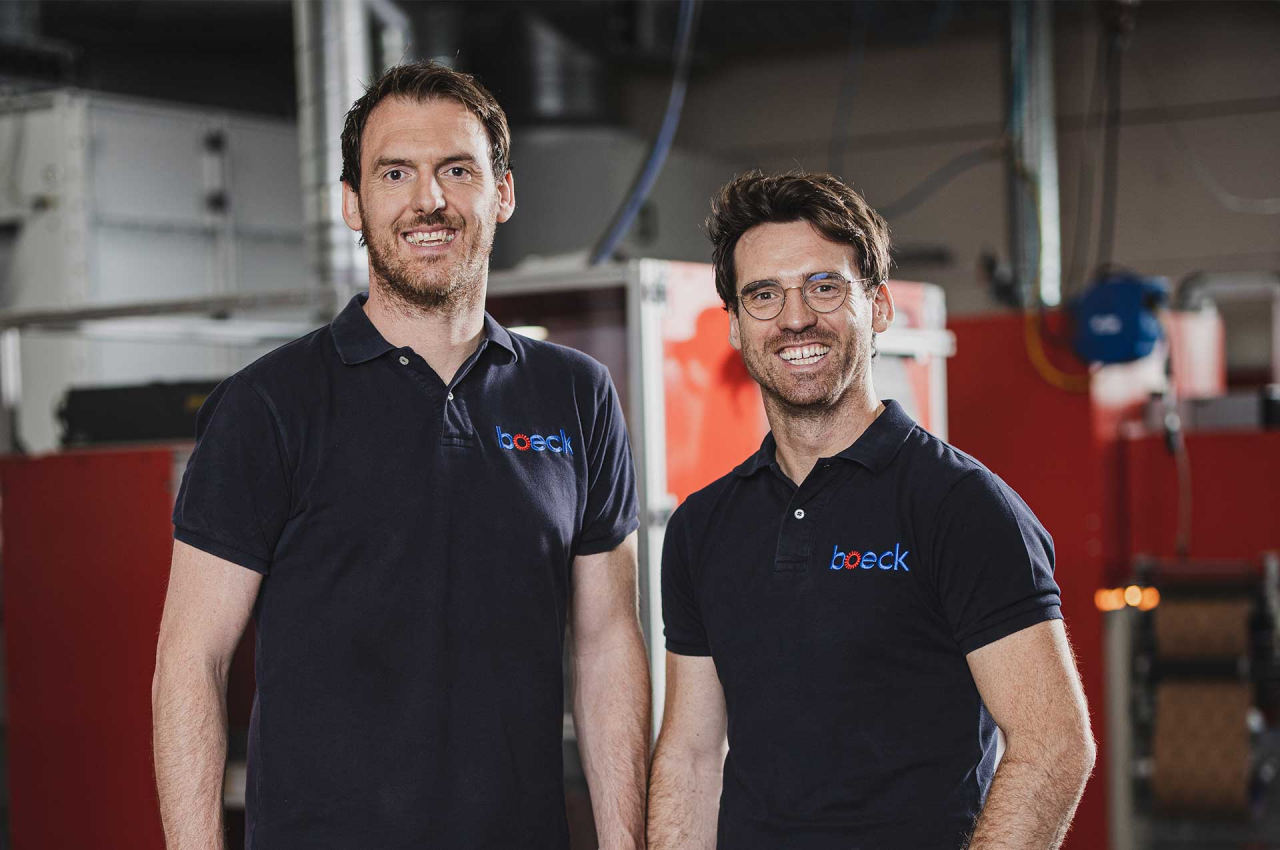
the latest deslagging technologies
the latest deslagging technologies
boeck GmbH develops and manufactures state-of-the-art technologies for sheet metal processing including deslagging. On the one hand, tool development is based on the requirements of our customers, on the other hand, we carry out basic tests. In this way, we develop an in-depth knowledge of the influencing factors and their interactions in the sheet metal working process and translate this into solutions. In this way, you benefit from tools that are perfectly tailored to your needs and know-how about the optimum process parameters. Our tools are MADE IN GERMANY by highly qualified personnel and the use of state-of-the-art, highly integrated machining technologies. In terms of production goals, we achieve maximum efficiency, especially through the automation and continuous digitalization of administrative and technical processes.
We work tirelessly to provide our customers with the best possible quality and the most effective tools, customized in the shortest possible time.
OUR PRODUCTS ARE COMPATIBLE WITH COMMON MACHINE MANUFACTURERS
Arku | Authentec | Boere | Bütfering | Costa | DMC | EMC | Ernst | Finishline | Fladder® | Flex | Gecam | Heesemann | Houfek | Jonsen | Kuhlmeyer | Lissmac |
Loeser | Loewer | Madora | Mc Talleres | Metabo | Metalbrus | Midwest | Ming Ping | Murata | Niederberger | NS Máquinas | Peitzmeier | Pola e massa | Q-Fin | RWT | Salida | St. Link | Timesavers | Tripuris | VG Machine | Viet | Weber | Wöhler | Wolters
YOUR CONTACT PERSONS
MARC BÖCK
Dipl.-Ing. (FH) Dipl.-Kfm. (FH)
CEO
ERICH LIEDEL
Dipl.-Ing. (FH)
Plant manager