Oxide wheel by boeck
When sheet metal is cut using oxygen, an oxide layer forms on the surface. This layer must be completely removed to ensure optimal results in further processing. The boeck oxide wheel is specifically designed to efficiently eliminate this residue, delivering a perfectly clean and precise finish.
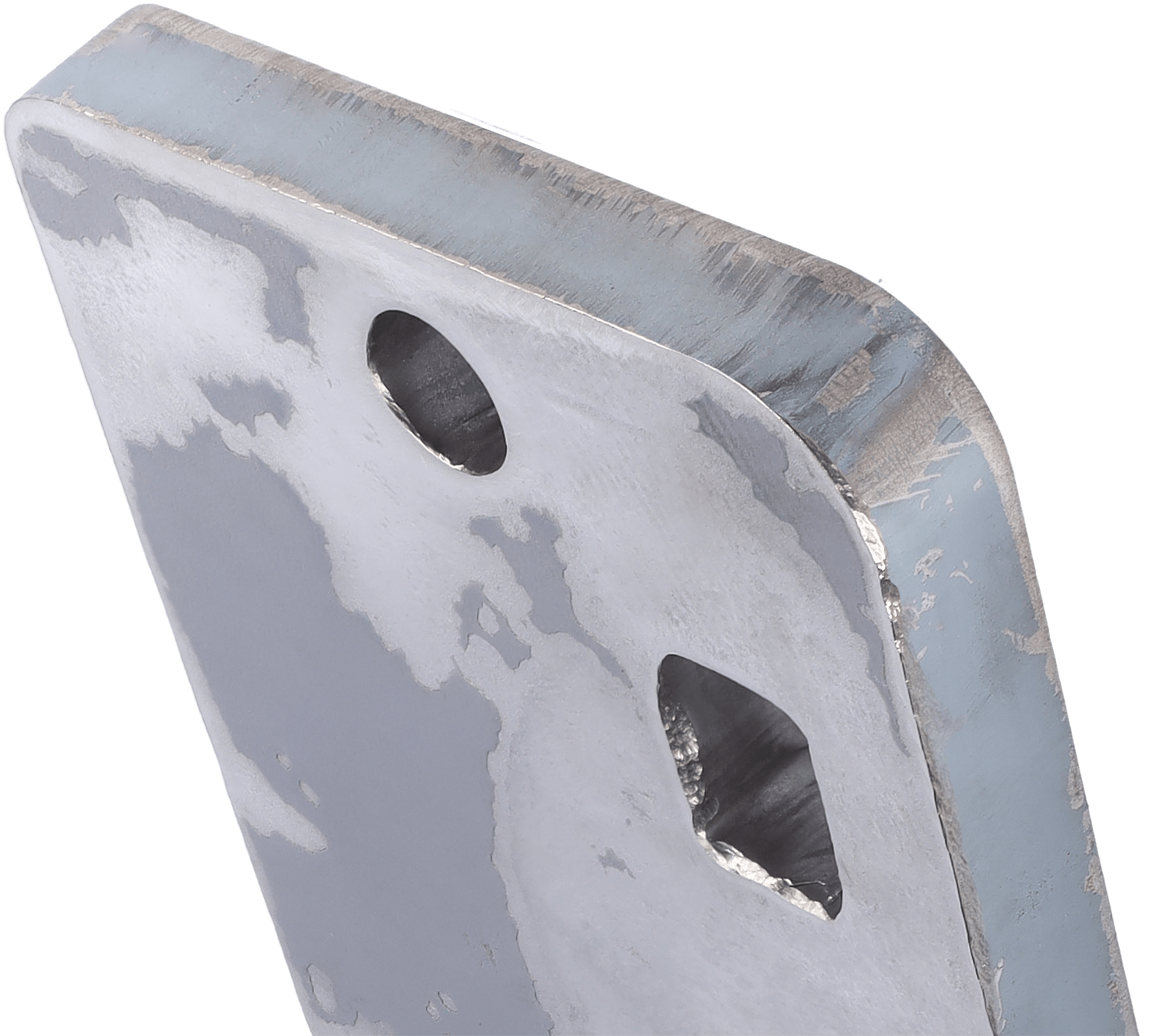
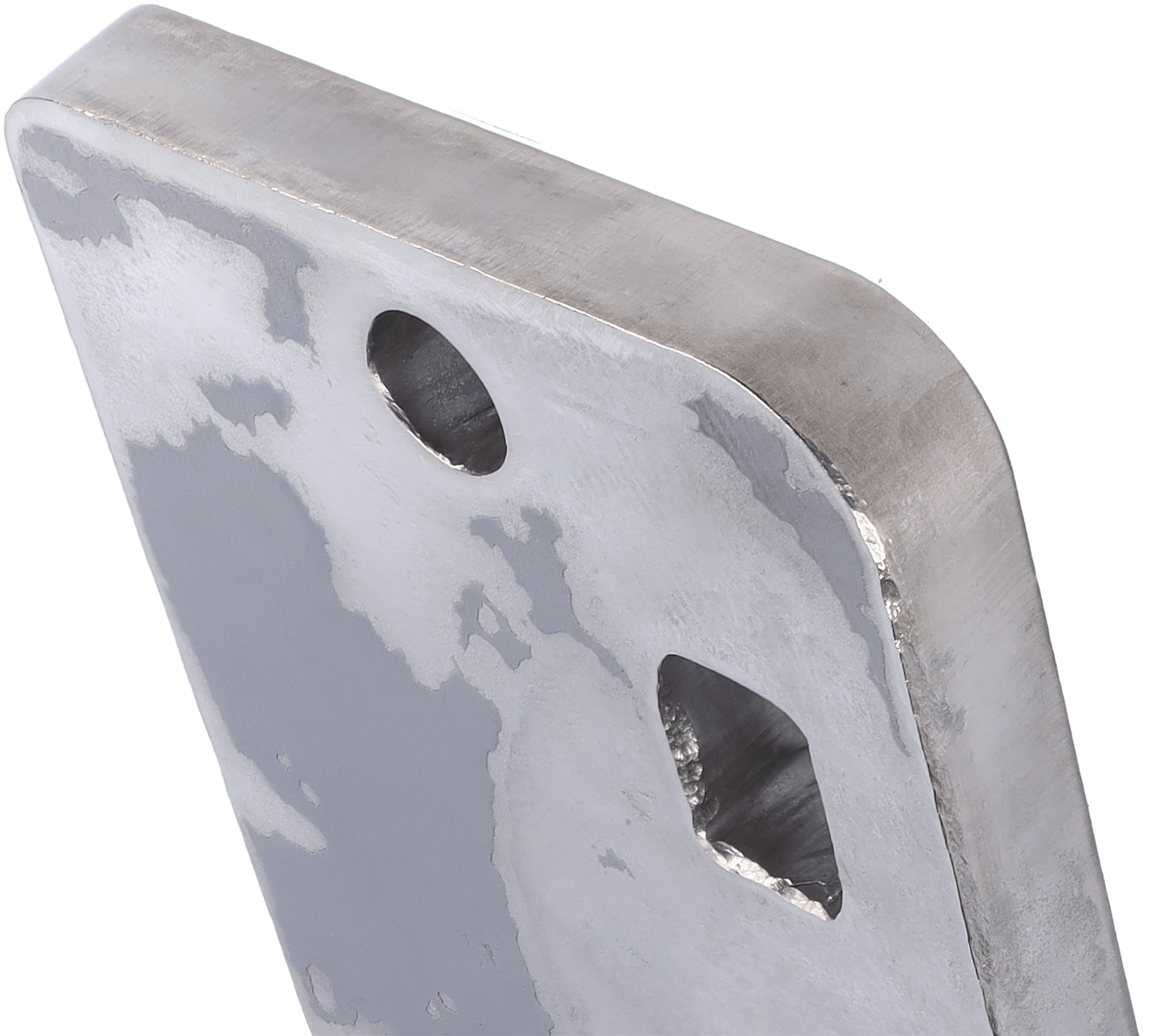
use of oxide wheels
Components cut with oxygen have oxide layers on the cut edges. These dark, bluish residues pose a problem for subsequent processes. If they are not removed, paint or weld seams may not adhere properly to the piece of sheet metal. It is therefore essential to remove the oxide layer for further processing. This is where the oxide wheels from boeck come into play. The flexibly mounted spring assemblies in a multi-row arrangement adapt to the component contours and achieve a bright metallic edge surface. They scrape off the unwanted layer and leave the workpiece ready for further processing.
The wheels are compatible with many machine manufacturers such as Lissmac, Loewer and Weber.
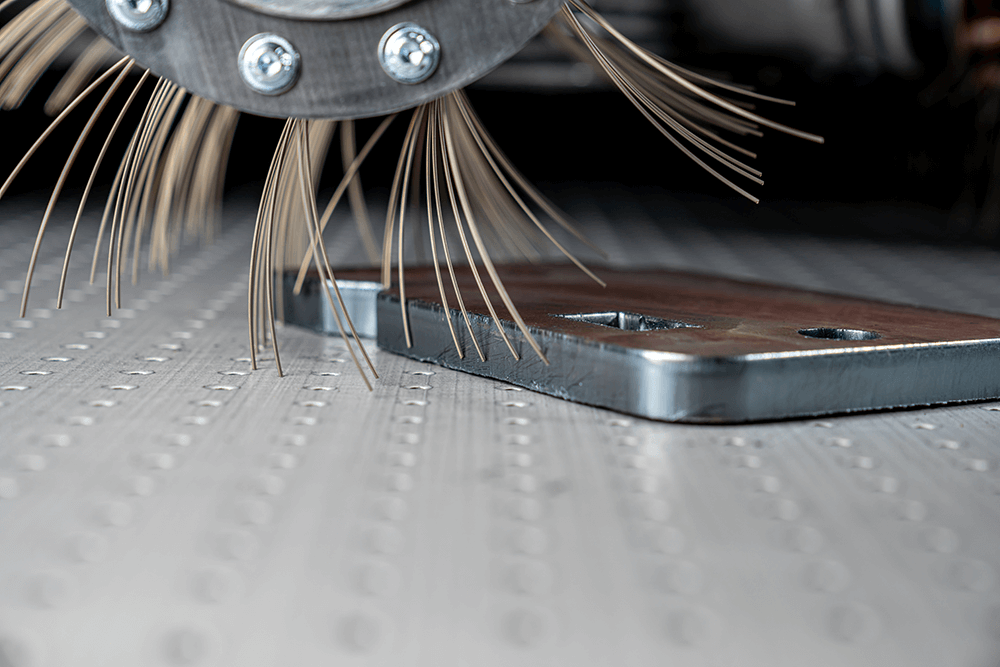
Our oxide wheel
Our oxide rollers make removing oxide layers effortless, thanks to their specially designed wire trim. They are compatible with standard automatic deburring machines, ensuring seamless integration into your processes.
With flexible customization options, boeck oxide rollers can be tailored to meet the specific requirements of your production at any time. Available in three different sizes, they offer versatility to suit a wide range of applications.
Need assistance in selecting the perfect oxide roller for your needs? Contact us—we’re here to help!
BOECK VARIABLE OXIDE WHEEL
Oxide wheels are an indispensable tool. However, when used in combination with deburring rollers, different levels of tool wear can occur, which can affect the efficiency and quality of machining.
To solve this problem, we offer an innovative solution: individually and infinitely adjustable oxide wheels. If your deburring wheels wear out over time, you can simply adjust the oxide wheels to a new size. This allows you to utilize the service life of your deburring rollers more efficiently.
The adjustable oxide wheels from boeck allow you to quickly and easily increase or decrease the diameter by up to 25 %. This gives you full control over the wear on your tools and allows you to optimize the productivity and quality of your processing.
Oxide wheel in Action
OUR PRODUCTS ARE COMPATIBLE WITH MOST MACHINE MANUFACTURERS
Arku | Authentec | Boere | Bütfering | Costa | DMC | EMC | Ernst | Famak | Finishline | Fladder® | Gecam | Heesemann | Houfek | Jonsen | Kuhlmeyer | Lissmac | Loeser | Loewer | Madora | Mc Talleres | Metalbrus | Midwest | Ming Ping | Murata | Niederberger | NS Máquinas | Peitzmeier | Pola e massa | Q-Fin | RWT | Salida | St. Link | Telefoncular | Timesavers | Tripuris | VG Machines | Viet | Weber | Wöhler | Wolters
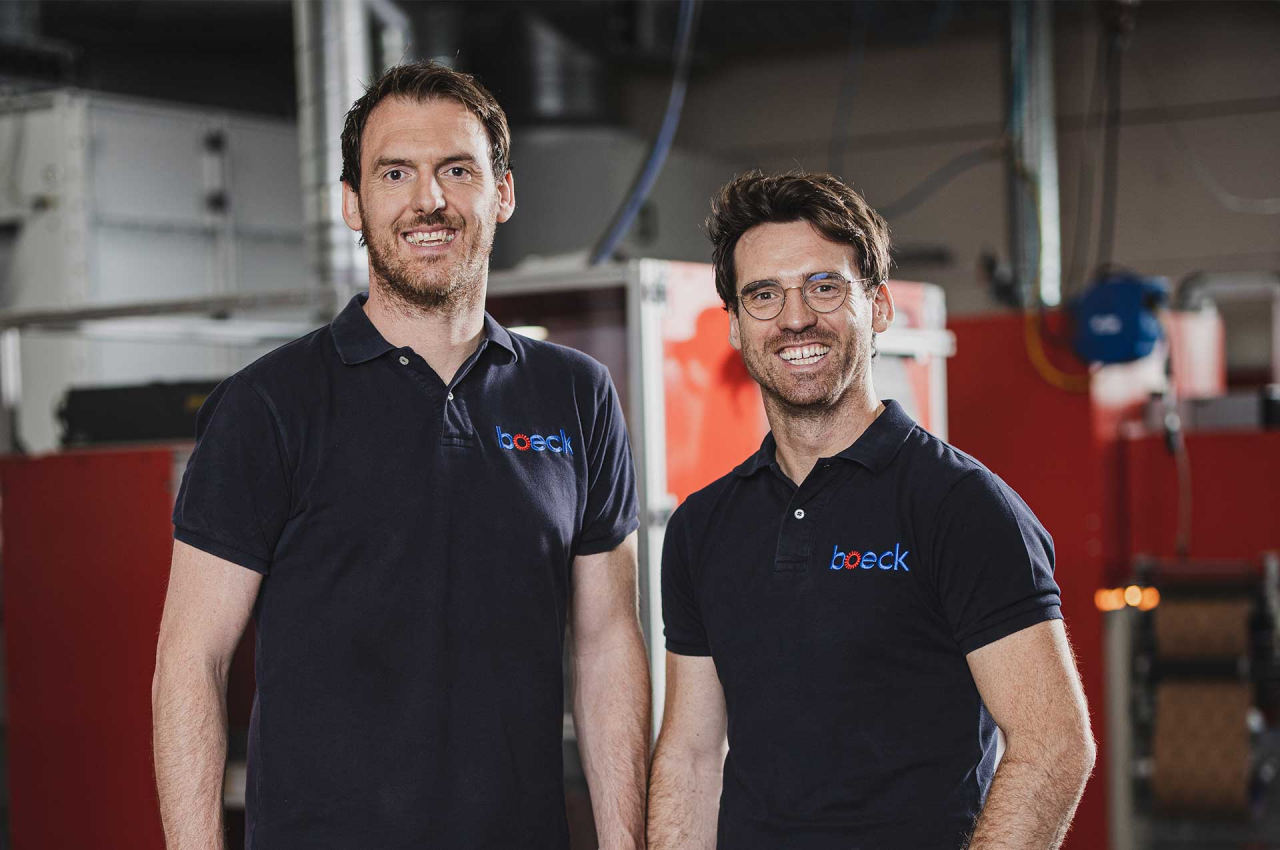
THE LATEST OXIDE REMOVAL TECHNOLOGIES
boeck GmbH develops and manufactures state-of-the-art technologies for sheet metal processing including oxide removal. On the one hand, tool development is based on the requirements of our customers, on the other hand, we carry out basic tests. In this way, we develop an in-depth knowledge of the influencing factors and their interactions in the sheet metal working process and translate this into solutions. In this way, you benefit from tools that are perfectly tailored to your needs and know-how about the optimum process parameters. Our tools are MADE IN GERMANY by highly qualified personnel and the use of state-of-the-art, highly integrated machining technologies. In terms of production goals, we achieve maximum efficiency, especially through the automation and continuous digitalization of administrative and technical processes.
We work tirelessly to provide our customers with the best possible quality and the most effective tools, customized in the shortest possible time.
OUR CUSTOMERS' BENEFITS
SAVINGS IN PROCESSING TIMES
Processing times can be reduced by tailoring the tools to fit customers' machines and projects. One customer application shows, that 80% processing time can be saved during deburring.
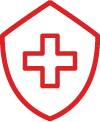
ENSURE SAFETY
Reduce labor intensity, ergonomic strain, and other hazards associated with oxide removal by eliminating manual oxide removal or the use of heavy chemicals.
OPTIMIZING OF OXIDE REMOVAL
Our task is to optimize the entire process chain, from oxide removal to finish grinding. We use the latest know-how and manufacturing technologies for our tools.
YOUR CONTACT PERSONS
MARC BÖCK
Dipl.-Ing. (FH) Dipl.-Kfm. (FH)
CEO
ERICH LIEDEL
Dipl.-Ing. (FH)
Plant manager